New Technology To Deliver Massive and Low-Cost Housing
- technocraft industries
- Aug 20, 2018
- 3 min read
If I were building on flat land, I would have delivered the houses even earlier. The neglected terrain is derailing me because I have to raise gab ions to keep the ground, but by December I will give the keys to the buyers, "he said.
A woman at the door who sells food to the builders on the site says that she thinks a miracle is happening there.
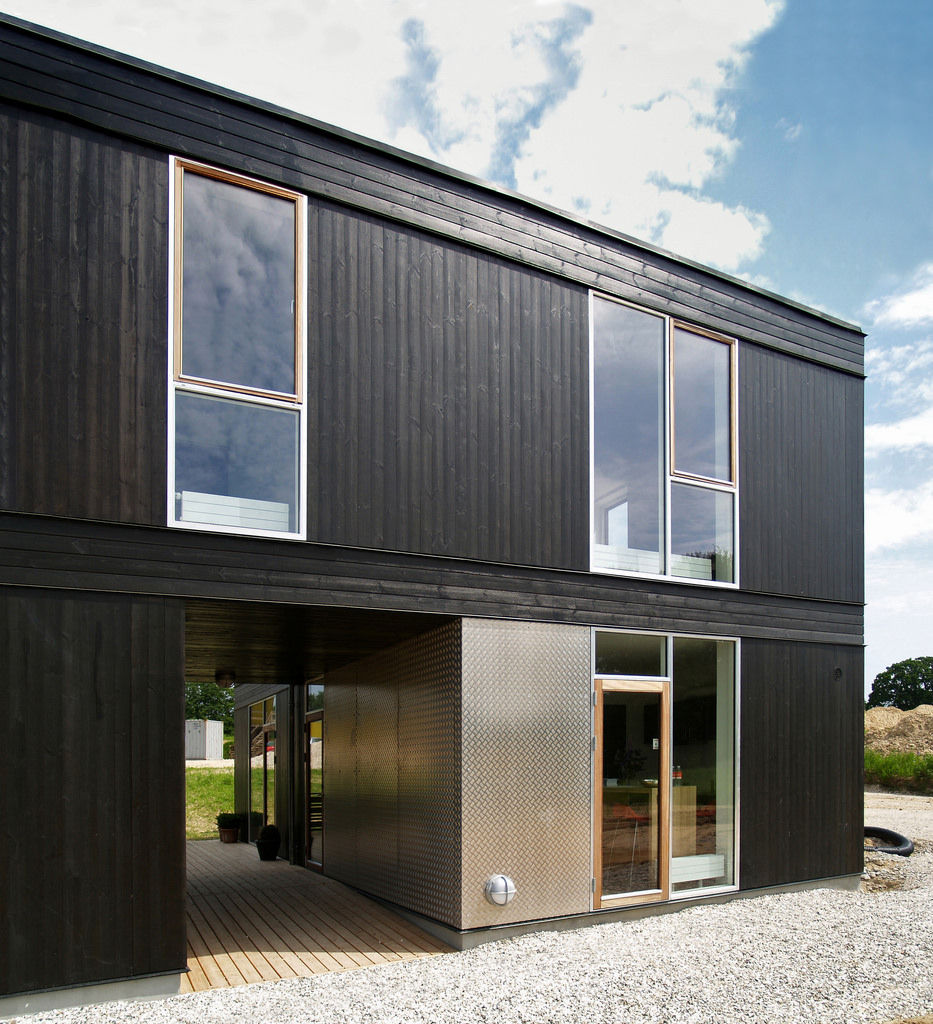
"One day there is no house on the site, the next day you wake up to find houses," she says.
Related content
Student hostels the new frontier for foreign investors
The real estate sector stimulates the growth of Kiambu Road
Investing in rural areas is complicated
Investors take advantage of the expansion of Waiyaki Way
Unknown to her is that the developer of Iguta Paradise has taken a paradigm shift from conventional construction techniques that would otherwise consume a lot of time to a more efficient reinforced concrete technology imported from Korea and the United States.
Configuration of aluminum formwork modeling for a perimeter fense. In the background there are shells for Iguta Paradise Homes built with alluminuim formwork from Korea. PHOTO | DELFHIN MUGO
He is using aluminum, steel, ballast, sand and cement panels. On the site, there are no construction stones or wood. The houses are built with aluminum panels from Korea, while the perimeter walls that separate the different units are being assembled with aluminum formworks modeled on the technology of Wall-Ties and Forms Inc. (WTF), a global giant based in Kansas. City in aluminum forming systems.
According to Thomas Muturi, architect and representative of the branch of WTF in Kenya, this reinforced steel concrete on site is basically a construction technology in which aluminum formworks are made that take the shape of the entire building, then assembled in the place, leaving a gap between the place where the ready-mix concrete is poured. This eliminates the need for brick and mortar.
Developed in the mid-1970s, the technology of using aluminum forms has been used in the construction of thousands of residential units for low and high-rise buildings.
He has proven successful in building low-cost massive housing projects in various parts of the world.
In Ghana, for example, a leading housing developer in collaboration with Social Security and the National Insurance Trust of the country built 1,680 apartments and sold almost all in less than two years.
In Kenya, no one understands the magic of this technology better than Epco Builders Ltd. Epco's 315 low-cost housing for Ministry of Housing employees along Jogoo Road is a good example. They began to use the traditional methods of construction of poles and beams in early 2010; the project took too long to deliver each block of flats; a level of 600 square meters of seven floors was taking a month to complete.
But when the contractor used the concrete formation of post and aluminum beams, the delivery speed was increased so much that a complete block of 35 planes was made in 10 weeks.
But it is the second housing project of Epco in Langata which clearly demonstrates the speed at which the formation of aluminum concrete can offer a house.
"We built 116 units in nine months, typically we were delivering one floor every four days, which means we were building a block that has four floors in just 16 days," says Mr. Muturi, whose WTF had partnered with Epco Builders Ltd to execute this project in February 2012. METICULOSAL PLANNING
The objective of this technology is mainly to industrialise the entire construction process. The way in which this technology achieves the goal, says Kilonzo, is ensuring that every time there is a continuous activity on the site.
This requires meticulous planning since Mr. Kilonzo explains:
"You have to implement the program in such a way that at each stage there is a different activity on the site, so the excavators would have to be on the site probably a month before, after which the masons will lay the foundations. Link the reinforcing steel and others to make the piping and wiring systems.Basically, from the assembly to the pouring of the concrete, we only need a day, depending on the size of the building ".
Although the slabs must be cured during the recommended 21 days, the use of high strength cement with this technology ensures that the walls dry quickly.
This means that around 90% of the aluminum mold is a slab, and ensures that there are no downtimes during construction.
ความคิดเห็น